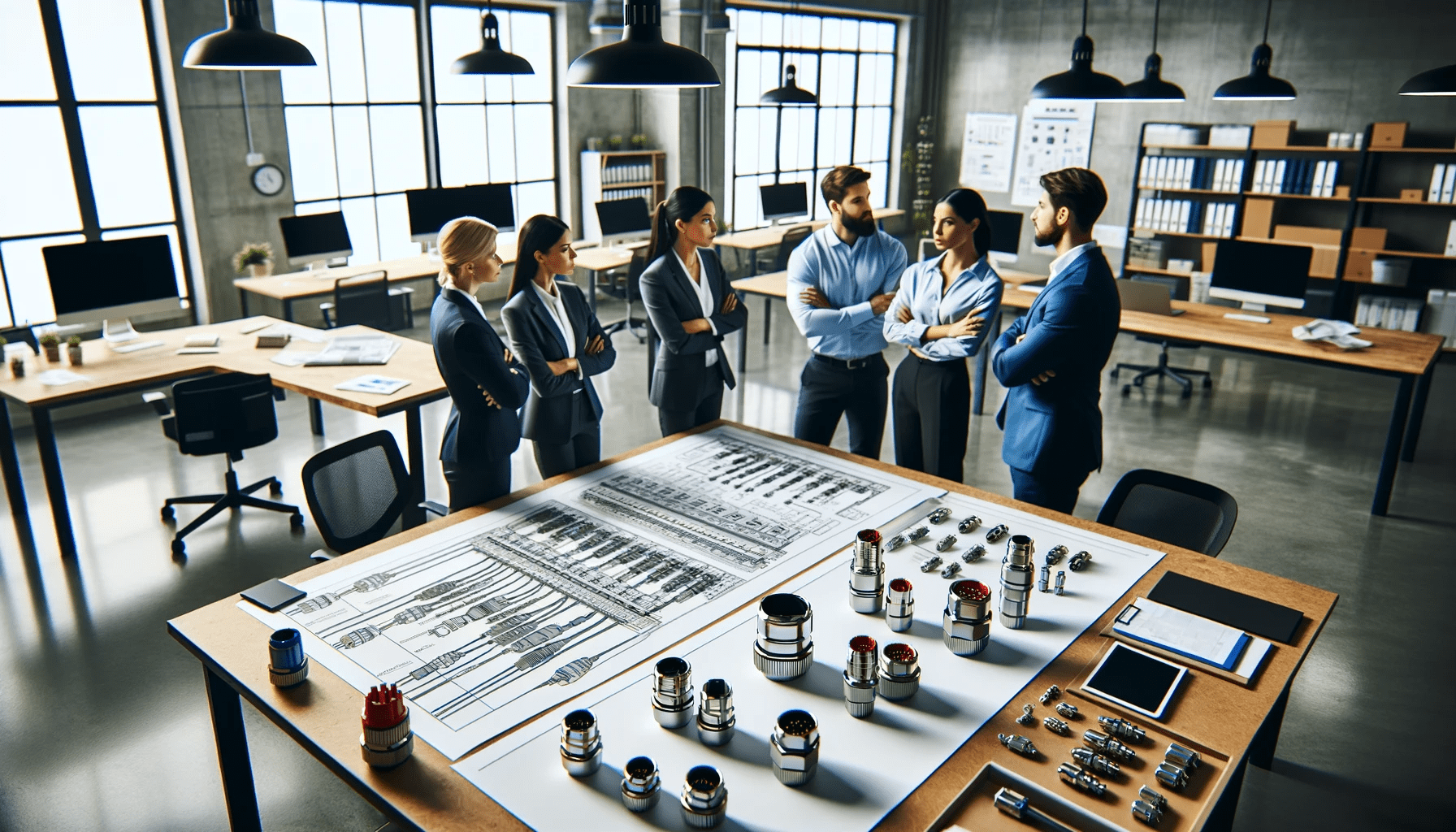
Exploring Alternatives to Camlock Connectors: A Comprehensive Guide for Industry Professionals
Introduction
The world of industrial connectors is evolving rapidly, with camlock connectors being a staple in various applications. However, the quest for more efficient, safer, and cost-effective alternatives is ongoing. This article delves into the intricate details of camlock connectors, their limitations, and the emerging alternatives reshaping the industry.
Understanding Camlock Connectors
Camlock connectors, known for their simplicity and reliability, are ubiquitous in industries where quick and secure hose and pipe connections are essential. These connectors are designed for easy handling, allowing for quick connect and disconnect without the need for complex tools or specialized skills. Typically made from materials like stainless steel, aluminum, and polypropylene, they cater to various applications, from petroleum handling to agricultural irrigation.
Despite their advantages, such as ease of use and a secure connection, camlock connectors are limited. These include potential compatibility issues with certain chemicals, temperature sensitivity, and a fixed orientation that might not suit all applications.
Why Look for Alternatives?
The industrial world is constantly evolving with the demands on connection systems. In scenarios involving extreme temperatures, corrosive materials, or the need for a more flexible orientation, traditional camlock connectors may need to be revised. Additionally, the pursuit of improved safety standards and cost-efficiency drives the search for better alternatives.
Types of Camlock Connector Alternatives
As industries advance, so do the alternatives to traditional camlock connectors. Some notable alternatives include:
- Twist-Lock Connectors: Offering enhanced security, these connectors use a twisting motion to lock, making accidental disconnections less likely.
- Bayonet Connectors: Known for their quick and easy push-and-twist locking mechanism, these are ideal for applications requiring frequent connections and disconnections.
- Threaded Connectors: Providing a more robust seal, these connectors are suitable for high-pressure applications.
- Magnetic Connectors: These innovative connectors use magnetic forces for connection, significantly reducing the time and effort required for hose or pipe connections.
Each alternative has unique advantages, catering to specific needs and applications. For instance, magnetic connectors offer unparalleled ease of use, making them ideal for applications where speed is of the essence.
Key Factors to Consider When Choosing an Alternative
Selecting the right connector alternative involves carefully considering various factors. Some key aspects include:
- Durability: The material and design must withstand the specific environmental conditions of the application.
- Compatibility: The connector should be compatible with the media it will be handling, be it fluids, gases, or solids.
- Ease of Use: Consider how easily the connector can be engaged or disengaged, especially in emergencies.
- Safety: The connector should minimize risks of leaks or disconnections, ensuring a safe working environment.
- Cost: Factor in the initial investment and long-term maintenance costs.
By carefully evaluating these factors, industries can make informed decisions that enhance efficiency and safety while keeping costs in check.
While camlock connectors have served industries well, the emergence of alternatives offers new opportunities for efficiency and safety improvements. Understanding the strengths and limitations of these alternatives is crucial for making informed decisions in a constantly evolving industrial landscape.
Innovations and Future Trends in Connector Technology
The connector industry is not just about replacing old with new; it’s about innovation and anticipating future trends. Recent advancements in materials science and engineering have paved the way for connectors that are more efficient and adaptable to challenging environments. For instance, developing connectors with smart technology capable of monitoring and reporting flow rates and potential leakages is on the horizon. These innovations are expected to improve safety in various industries’ ds and operational efficiencies in various in.
Another exciting trend is the integration of IoT (Internet of Things) with connector technology. Imagine a connector that serves its primary function and collects and transmits data about the system’s performance. This advancement could revolutionize maintenance strategies, moving from reactive to proactive and predictive maintenance.
How to Make the Transition
Transitioning to new connector technology requires a strategic approach. It’s not just about the technical swap; it involves understanding the implications on existing systems, training personnel, and ensuring a smooth integration. Here are some steps to consider:
- Technical Compatibility: Assess the compatibility of the new connectors with existing equipment. This includes checking for size, material compatibility, and pressure ratings.
- Staff Training: Ensure that staff are adequately trained on the new connectors. Understanding the mechanics, safety protocols, and maintenance requirements is crucial for a successful transition.
- Phased Implementation: Consider a phased approach to implementation. Start with a small, controlled environment before rolling out across the entire operation.
- Monitoring and Feedback: Continuously monitor the performance of the new connectors and collect feedback. This will help identify any issues early on and make necessary adjustments.
By taking these steps, industries can ensure a smooth transition while maximizing the benefits of the new connector technology.
The exploration of alternatives to camlock connectors is not just a matter of replacing one type with another; it’s about embracing innovation and adapting to the evolving needs of various industries. As we have seen, each alternative brings its unique set of advantages, catering to specific requirements. The key lies in understanding these alternatives, considering the factors that matter the most, and being prepared for future trends. With the right approach, the transition to these new technologies can lead to improved efficiency, safety, and cost savings, ultimately contributing to the growth and success of your operations.